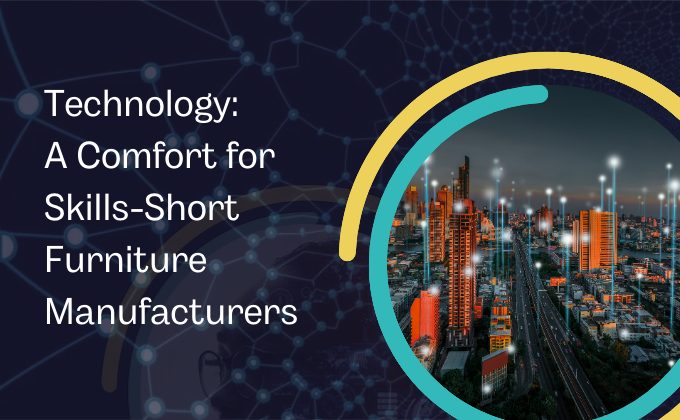
A solution that’s right at home for your business
Furniture retailers are increasingly under pressure from customers to deliver shorter lead times, in turn passing on the challenge to manufacturers of furniture, fittings and door furniture. The subsequent rate of growth leaves furniture manufacturers with gaps within their current solution and over purchase on materials due to inaccurate forecasting. A furniture manufacturing ERP solution from SYSPRO allows you to meet these challenges.
The product configurator offers rule-based product customisation allowing you to meet customer specifications in a controlled, cost-effective and friendly manner. SYSPRO allows you to respond to daily changes in scheduling priorities and material requirements, reducing waste through accurate forecasting. The SYSPRO CRM solution allows tracking and management of all customer and supplier touch points, while SYSPRO’s mobile technology, Espresso, means you’re always on top of stock movements and distribution.
How SYSPRO ERP can help your business
Increase Sales and Mange Demand
- Provide employees with mobile access to information anytime, anywhere
- Manage complex pricing such as contract pricing, volume discounts, promotions and rebates
- Reduce paperwork with Electronic Data Interchange (EDI) to automate order processing
- Ensure customer satisfaction by effectively controlling the return and exchange of items with full visibility and tracking until the transaction is concluded
- Improve efficiency with repeat order customer templates
Optimise Supply Chain
- Purchase more strategically with data-driven forecasts based on history, seasonality and supplier lead times
- Gain visibility to streamline MRP processes and optimise inventory
- Leverage advanced forecasting and planning to more closely match supply with demand
- Streamline purchasing workflow with seamless electronic trading
- Manage returns and exchanges of supplies and materials more efficiently
Streamline Production
- Generate accurate specs quickly for highly customisation products with a rules-based Product Configurator
- Manage design changes and related costs with Engineering Change Control
- Minimise bottlenecks and keep up with seasonal demand with advanced planning and scheduling software
- Track shop floor operations and gain work-In-progress visibility in real time to optimise labour
- Support product kitting across hundreds and thousands of SKUs
Enable Strategic Financial Management
- Streamline management of revenue, payables, receivables and cash flow across multiple languages and currencies
- Simplify compliance with global and local financial regulations, such as International Accounting Standards (IAS), GAAP and International Financial Reporting Standards (IFRS)
- Make better decisions by performing what-if analysis of accurate financial data
- Improve visibility into total costs to identify savings opportunities
- Gain better insights into buying and supplier trends, by customer and by product
Best-in-class Furniture Software
Manufacturing operations management for your unique business
Without solid control over your operational and financial processes, you run the risk of production mistakes, late deliveries and out-of-control costs that hurt your margins. Whether you’re selling high-end custom chairs or cabinet drawer pulls – spreadsheets can only take you so far.
SYSPRO ERP Software is built to solve challenges across your entire furniture and fittings manufacturing operation. Yet, they are completely flexible and customisation, too. Just like your customers, you can choose the design that suits your business best.
Take your organisation to the next level of growth with a strong, integrated ERP technology foundation, from a vendor who knows how to solve your specific industry challenges.
What our customers say about SYSPRO
Want to see SYSPRO ERP in action?
Actions speak louder than words so why not let us show you what our solutions can do. Our consultants can come to you and we’ll be able to give you a live look at how our software works and how it will help you make better business decisions.