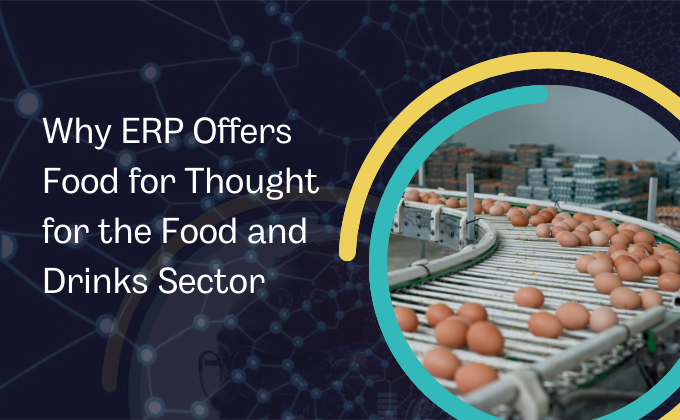
Getting things done: Our recipe for success
Food and beverage manufacture is the process of taking raw ingredients and transforming them, by chemical or physical means, into food for the convenience of the consumer. Food and beverage ERP supports an industry that supplies most of the food consumed worldwide. Only self-sufficient farmers who eat what they grow can be considered outside of the modern food and beverage industry.
Not only do consumers now demand more variety and innovation from food manufacturers, but also show a growing concern for quality and source of the ingredients used; meaning documentation and traceability has never been so important. To juggle this with low profit margins and perishable ingredients and stock mean food and beverage manufacturers often need a superior ERP solution.
SYSPRO integrates manufacturing, accounting and distribution processes to create an overall more efficient operation so data needs only to be entered once. Inventory management accurately forecasting stock requirements through seasonal and industry trends combined with previous order data to keep stock levels proactive rather than reactive, keeping waste to a minimum.
How SYSPRO ERP can help your business
Faster Time to Market
- Apply discipline to managing recipes throughout development with revision auditing
- Know what ingredients are included in each order with robust batch and lot tracking
Optimise Supply Chain
- Meet company goals for ingredient and raw material sourcing
- Purchase more strategically with an eye on seasonality
- Improve forecast accuracy for just-in-time production
- Enhance materials and inventory management to maximise shelf life and reduce waste
- Improve visibility into buying and supplier trends with built-in business intelligence reporting to facilitate Value Stream Analysis
Streamline Production
- Manage bottlenecks and keep up with seasonal demand with simpler production scheduling tools
- Enforce accuracy with automated production of labels, barcodes and RFID tags
- Track your shop floor in real time and reduce lead times for faster delivery
- Drive efficiency using Electronic Data Interchange (EDI) with trading partners
Solve Compliance Challenges
- Meet Food Safety Modernisation Act (FSMA) and Safe Quality Food (SQF) standards with forward and backward traceability of lots/serials and supplier ingredients
- Streamline USDA, HACCP, GMP and other regulatory requirements with fully integrated processes based on raw materials receiving, production, packaging or shipping steps
- Automate documentation requirements and mitigate litigation expenses
- Reduce risk even further with electronic signatures and full audit trails
Enable Strategic Financial Management
- Streamline accounting operations
- Gain visibility into trends with built-in sophisticated analytics and reporting
- Optimise profitability with end-to-end costing analysis
- Support multiple currencies and sites with ease
Boost Customer Service
- Get a single view of customers, contracts and orders with integrated CRM
- Exceed customer expectations and improve margins with more accurate quoting
- Manage and track special customer pricing
- Reduce time-consuming reconciliations and improve accuracy with trade promotions management functionality
Best-in-class Food ERP Software
Manufacturing operations management for your unique business
Regardless of what products you produce, spreadsheets can only take you so far. You need management tools designed for your business to maximize operational effectiveness, minimize spoilage and ensure food safety.
Unlike entry-level accounting software, SYSPRO ERP Software for food is built to solve challenges across your entire food manufacturing operation, while being completely flexible, customisation and extensible. Choose the flavor that suits your business best.
Take your organisation to the next level of growth with a strong, integrated technology foundation from a vendor who knows how to solve your specific industry challenges.
What our customers say about SYSPRO
Want to see SYSPRO ERP in action?
Actions speak louder than words so why not let us show you what our solutions can do. Our consultants can come to you and we’ll be able to give you a live look at how our software works and how it will help you make better business decisions.